
Increase Throughput and Reduce Worker Burnout
The MWES engineered, turn-key pack out system has a number of benefits for the consumer products production facility from increasing production speeds to packaging quality and repeatability, to ease of implementation of an automated system.
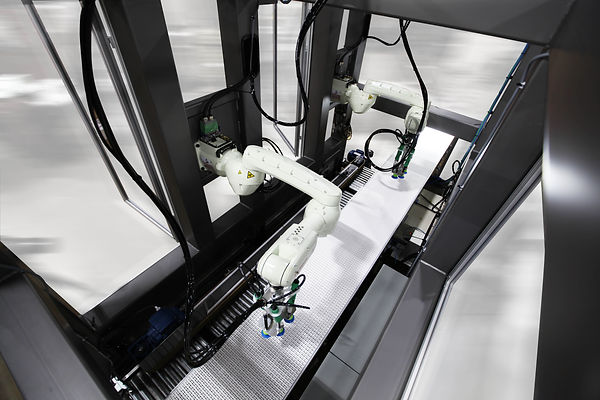
In terms of production speeds, a MWES pack out system with three pick-place robots can fill boxes at a rate of between 120-160 packages per minute. This performance is roughly equivalent to the speed at which 3-4 dedicated human hand packers could provide while offering more consistent performance and quality. The self-contained system also offers adjustability for a variety of different sized bags as well as the ability to pack them in precise pack patterns. As a robotic system, it can perform at this pace for all three shifts without rest and could be configured to run in most cold rooms.
​
From the start, the MWES pack out system was designed to integrate into existing production lines including tight floor space applications. All aspects of the machine, from robots to control systems, are housed within the system’s frame. The system only requires power and production line connection to operate once the machine is placed in the facility. Sometimes installation can be completed in as little as a day. Its compact footprint also allows for more placement options on the production floor and the potential for recovering valuable floor space.
​
With quality labor becoming scarce, wages rising and profitability tied so closely to production efficiency, the MWES pack out system makes sense for firms that are searching to find the most streamlined packaging processes. Adding MWES’ 24/7 service, the combination of equipment and support creates the winning choice for CPG packaging operations.