3 Ways Preventative Maintenance Can Save You Money
- Midwest Engineered Systems
- Nov 10, 2015
- 3 min read
Updated: Sep 26, 2018
Providing preventative maintenance for an automated system is an easily forgotten and neglected task. There is so much hustle and bustle occurring in any given day, and if the equipment is working, minor repairs or adjustments can often go overlooked.
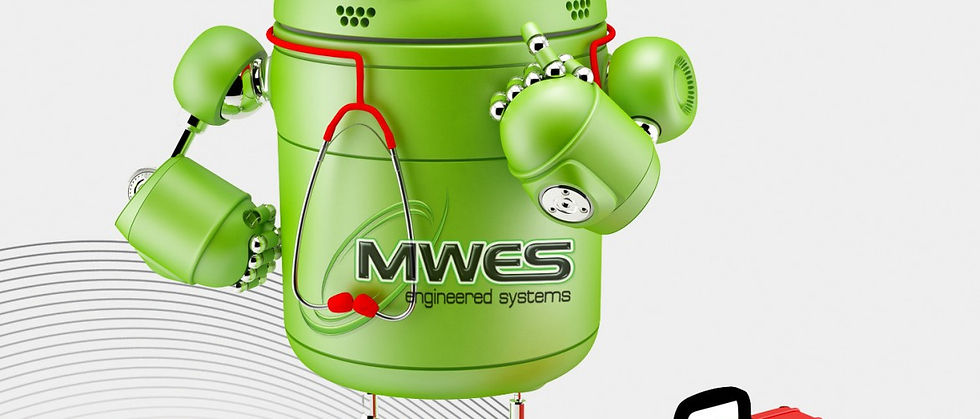
Preventative maintenance is required for consistent upkeep of your automation equipment in order to reduce every day wear and tear and eliminate unexpected breakdowns. The objective of preventive maintenance is to identify and resolve problem areas that negatively affect the productivity of your robotic automation systems. Although a system may be operating just fine, there are a number of benefits to regular preventative maintenance, including saving money. Below are three examples of how this can help reduce costs:
#1 Limits Breakdowns
Nothing is worse than having your automated system malfunction in the middle of a big project, especially when the problem could have been avoided in the first place. Everything will have to be delayed, while time and energy is spent trying to fix the issue. The situation may increase stress levels, frustrate employees, and irritate clients. On top of it, actual breakdown costs for automated systems are usually 4-5 times more expensive than the maintenance costs themselves. Lack of maintenance can contribute to premature failure, which can result in expensive downtime.
#2 Increases ROI
All robots and automated equipment develop wear and tear over time and require periodic maintenance, so maximizing your system's usable life makes sense both from a production and fiscal perspective. Waiting until your equipment shows signs of failure, even a small component issue, can create a ripple effect of major, long-term problems. If your system is not producing parts, you are not making money. With proper maintenance, you get the maximum life out of your equipment.
#3 Increases Efficiency and Speed
If you eat healthy, get enough sleep, and stay physically active, you are more likely to feel better and perform better in your daily life. The same can be said about your automated equipment. If your system has a firm maintenance program where adjustments, cleaning, and problems are fixed regularly, it is likely to produce a higher quality result at a quicker pace.
Maximize the Life of your Equipment
Implementing preventive maintenance practices doesn’t have to be complicated. Many times, it only requires quick daily inspections or in-depth check-ups on an interval basis. Taking the time to make maintenance a priority will help you gain control over your equipment’s life and avoid major downtime, which can have a big impact on your profitability.
Preventative Maintenance with MWES
On a periodic basis, our Automation Technicians will perform up to 60 checks and services on your robotic automation systems. A comprehensive report will outline any problems that have the potential to cause unexpected downtime with the system. This document will be used as the basis to prioritize our ongoing action plan. We recommend this service to be performed no less than annually to minimize unexpected downtime.

Experience has proven it is much more cost-effective to perform preventive maintenance on a regular schedule than to wait for a failure.
We will address cell safety, cable management, mechanical, electrical, process equipment, and the robot controller and software. Items included with this service include cleaning supplies, replacement light bulbs, wire ties, filters, and backup batteries.
Midwest Engineered Systems offers state-of-the-art service for your automated, robotic, and web handling equipment. We service all major brands and staff experienced field technicians that can solve any automation issue.
Komentar