

Automation Process Development
Teaming Up With Our Customers to Link the Divide Between Design and Production
Our approach to automation process development is to first evaluate your current operation or your process assumptions and evaluate speed, quality, and other process results. We work with you to establish requirements, goals, and risk thresholds for the new prototype process all the way to the development of a turnkey production line. 3-4 testing options are brainstormed by our engineering team and presented to you. A fixed bid is then put into place which includes the evaluation of the prototype and a report of our findings. Processes are tested and analyzed to determine if the prototypes meet the necessary results such as up-time, through-put rates, quality, and process capability requirement.
Process Development Can Improve Manufacturing By:
-
Reducing product cost
-
Reducing equipment cost
-
Improving process quality
-
Increasing process speeds & consistency
-
Improving overall equipment performance

Related Capabilities
Additive Manufacturing
Control Systems
Data Collection Systems
Laser Processing
Assembly
Break Press Automation
Robotic Rough Machining
Off-Line Programming
Automated Guided Vehicles (AGVs)
Vision Inspection and Test
Wash Systems
Process Improvements
Process Improvements include evaluation of current equipment capability and determination for implantation of new sensors, controls, and methods to improve manufacturing.
​
Controls Updates
Process improvements are offered to optimize your current equipment to improve functionality and to increase the life of your system. These improvements typically involve custom developed software and current controls hardware that improves tasks and processes.
Benefits to Process Improvement & Controls Updates
-
Increased Return-on-Investment
-
Lower up-front investment vs. buying new
-
Improved part throughput
-
Increased quality
-
Increased equipment life
PROCESS DEVELOPMENT WORKFLOW
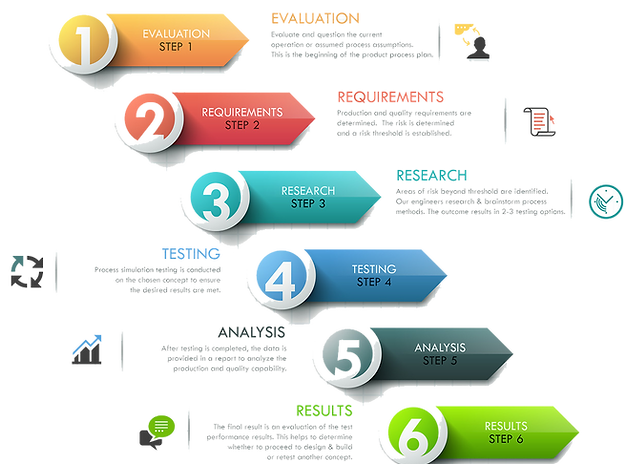