
AS/RS System Benefits
AS/RS buffer systems for the production environment
For the longest time, the benefits of Automatic Storage and Retrieval Systems (AS/RS) have been in the sole domain of large warehousing applications, but there’s significant benefit to be had using AS/RS systems in production environments, if they could be designed with manufacturing needs in mind.
MWES has done just that.
Our production-focused storage systems are designed from the start to fit into legacy production facilities. With its scale and operation, our AS/RS system can change how you think about not just warehousing but production processes - and increase your throughput along the way.
We’ve broken out below some of the biggest ways a production-focused AS/RS system can streamline the way a manufacturing facility operates.
More efficiently store tooling and jigs
No more hunting around the shop – or worse searching the stock yard - for occasionally used tooling. MWES’s automated storage and retrieval system can organize seldom used but necessary jigs and fixtures in a system that makes it quick to locate and access when needed while freeing up valuable floor space when not.
Square footage is highly sought after but rarely is the cubic footage of a shop considered fully. The MWES system is designed to go high and maximize the utility of your facility’s ceiling heights. The system is able to store things in a high density format that stacks inventory vertically,
maximizing floor space.
All this equates to more efficient production changeovers as fixtures are stored in a known and easy to retrieve area rather than relying on operator notes and memories. It also makes sure the jigs and tooling are placed away from the potential for damage by any manner of incidents, reducing potential lost time and cost incurred from fixing potential issues.
Maximize Floor Space
Store up rather than out. Our system is designed to be built within existing buildings. With its ability to store things easily up to 30ft in the air, the potential to double or triple the current storage capacity without having to add on or store off-site is certainly within reach.
Many of today’s shop floors are high density, making it difficult to get forklifts into places where tooling or materials are stored without getting uncomfortably close to critical production machinery. Add humans at the wheel, and the operation can become even more hair raising to floor management.
With MWES’s purpose-designed retrieval system, accessing materials stored at the higher levels doesn’t require maneuvering large forklifts for challenging picks or relying on human operators to perform these functions. The system’s compact size also reduces through-way congestion, as it doesn’t rely on maneuvering large masses like fork truck bodies to pick from the highest locations. Instead, it uses its own compact shuttle system to store and retrieve materials.
That extra floor space made available with the MWES AS/RS system opens up opportunities for expanding production space or streamlining workflows with more area for positioning equipment. The system may even be able to help keep greater material stock in-house to reduce work stoppages from running out of parts.
Manage Work in Progress
Reduce changeover time and increase production schedule efficiencies with efficient storage and retrieval abilities. Some production steps take longer than others. That disparity may manifest from shorter turn times on one machine while parts stack up waiting for longer processes on other machines.
MWES’s production AS/RS system can act as a production buffer by easily storing and retrieving WIP stock. This temporary storage ability opens up higher speed production machines for other jobs while slower processes work through backlogs, as well as keeping production areas cluttered and unorganized.
Being able to easily buffer stalled projects into the MWES storage system opens up floor space, machine time and reduces confusion. Using an AS/RS buffer system also frees resources to operate on other jobs without being bogged down by waiting for backordered materials, increasing overall production efficiency.
Clear out the receiving department and stage upcoming jobs
Sometimes materials for future jobs get stuck in Receiving. Then they can get lost or damaged. An AS/RS system can organize these materials in a manner that makes them quick and easy to retrieve in an organized fashion when the work begins. With the system’s ability to store vertically, incoming materials can be cataloged and stored in the AS/RS racking out of the way until needed.
A production-supporting automated storage and retrieval buffer system could also be used to prepare incoming jobs by staging components and tooling before work can begin. Having this organizational ability lends itself to more easily scheduling when both materials and tooling is delivered to the floor and when things should be returned.
An automated AS/RS buffer system also can help keep track of jobs that have all of its materials at the ready and which do not. These abilities make it easier for job schedulers and buyers by providing needed knowledge and flexibility that leads to greater production efficiency.
You can read more about the benefits of the AS/RS system right here.
Tight spaces and inefficient workflows can be reduced with safe and efficient material storage and retrieval systems. Contact us today to learn more about the MWES production-focused AS/RS and how we can streamline your manufacturing systems.
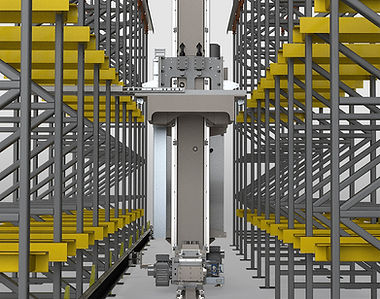