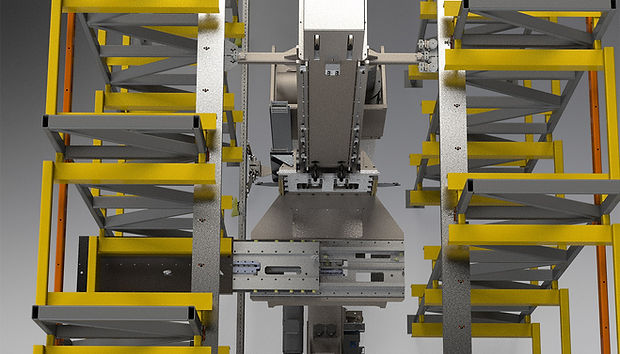
Components of the AS/RS
Automated Storage and Retrieval Systems (ASRS) are designed to help manufacturing and distribution plants store and retrieve items with non-palletized methodology. Midwest Engineered Systems integrates various technologies that can handle a wide variety of inventory types and volumes.
Three ASRS Types
ASRS types can be split into three general categories and seven specific technologies.
Shelf and Tray Picking—An operator receives a tray of the requested product in this type of picking.
Bin-Based Picking—An operator receives a single tote or bin in bin-based picking.
Robotic Picking—An operator receives goods from mobile robots operating in an enclosed shelving system.
Shelf and Tray Picking
Vertical Carousels
Vertical carousels are a series of chain-driven carriers. The carriers move in a bi-directional loop around a track. This ASRS delivers goods at slow- to medium-velocity to an operator’s work counter efficiently and ergonomically. Vertical carousels can effectively work with carriers that hold up to 1,650 pounds per carrier. These carousels can offer throughput rates of 100 to 400 lines an hour. Batching stations and light-directed picking technologies can result in even higher throughput rates.
Horizontal Carousels
Horizontal carousels consist of dense storage bins moving horizontally to an operator at slow- to medium-velocities. This carousel moves items and cases that weigh up to 200 pounds. These bins are usually installed in pods to maximize picking efficiency and throughput rates. Horizontal carousels provide both high storage density and high floor space utilization. Batching stations and light-directed picking technologies allow for throughput rates of up to 600 lines an hour.
Vertical Lift Modules (VLMs)
Vertical Lift Modules are the most versatile of the technologies mentioned in this category. The VLM is preprogrammed to automatically reconfigure itself as a facility’s inventory changes. This technology consists of two columns with inserter and extractor sections within the center. It can handle trays that can carry up to 2,200 pounds each. The VLM automatically identifies and retrieves stored trays from either column. Once retrieved, it delivers the trays ergonomically to an operator. VLMs can save up to 85 percent floor space and present between 125 to 475 items each hour to an operator.
Bin-Based Picking
Vertical Buffer Modules (VBMs)
Vertical buffer modules are a cost-effective solution for facilities that only require smaller storage and retrieval applications. The VBM is an enclosed shelving system that picks and stores bins via a movable mast that runs down a center aisle. A chief function of the VBM is to work ahead of an operator. It should optimize throughput rates by queuing up the next pick for the operator.
Crane-Mounted Mini-Load
Mini load systems are optimal solutions for handling lightweight manufacturing loads. A crane-mounted load handling technology operates in each storage aisle. Mini loads handle totes and trays that can weigh between 220 and 750 pounds. The cranes in each aisle use either wheels or rails to very quickly deliver products to a requesting operator. Mini loads are ideal for low throughput requirements. The system can deliver about one load each minute, resulting in around 60 to 100 lines each hour.
Robotic Picking
Floor Robots
In the floor robot system, inventory is stored on portable storage shelving that is transported to operator access areas using mobile, autonomous robots. Once the operator has the required product, the robot returns the shelf to its proper storage area. This system is suitable for slow- to medium-velocity inventory and for throughput rates of 100 to 300 lines an hour. The system’s throughput can be drastically improved simply by adding more portable robots to the system. The system can handle up to 1,000 pounds for each shelving system in its standard configuration. It can handle up to 3,000 pounds for each shelving unit when configured for heavy-duty.
Robotic Shuttles
Robotic shuttles travel autonomously between different levels on rails. They travel between storage areas at high velocities; they typically achieve throughput rates of 200 to 700 lines each hour. This throughput range can be increased simply by adding more robot shuttles into the system. The shuttles can carry trays and cases that weigh between 35 to 65 pounds. They require only minor modifications to handle a variety of business challenges.
With all the options and configurations available for ASRS installations, trust Midwest Engineered Systems to be your guide in designing and implementing a custom ASRS system that provides the throughput and efficiency your facility needs. Contact us today to learn more!